Fall arrest equipment is designed to protect workers by preventing them from falling to lower levels in the event of a slip or fall. Regular testing is crucial to ensure that this equipment functions as intended and meets the required safety standards. This will ensure the safety of individuals who work at heights: construction workers, window cleaners and maintenance personnel.
Occupational safety and health regulations stipulates the testing and inspection of fall protection equipment. Compliance with these regulations is not only a legal requirement but also an essential aspect of maintaining a safe working environment.
Fall arrest equipment is subjected to wear and tear over time due to exposure to the elements, repeated use and environmental conditions. Testing helps assess the integrity of the equipment, including straps, connectors, anchors, and other components, to ensure they remain in good condition.
Manufacturers provide guidelines and recommendations for the testing and inspection of fall arrest equipment. Following these recommendations is critical to maintaining the equipment’s performance and longevity.
Employers have a responsibility to provide a safe working environment for their employees. Regular testing and maintenance of fall arrest equipment demonstrate a commitment to safety, reduce the risk of accidents, and can help mitigate liability in the event of an incident.
Testing provides an opportunity for workers to become familiar with the proper use and inspection of fall arrest equipment. Training on the correct procedures for using and maintaining the equipment is crucial for ensuring its effectiveness.
Free consultation
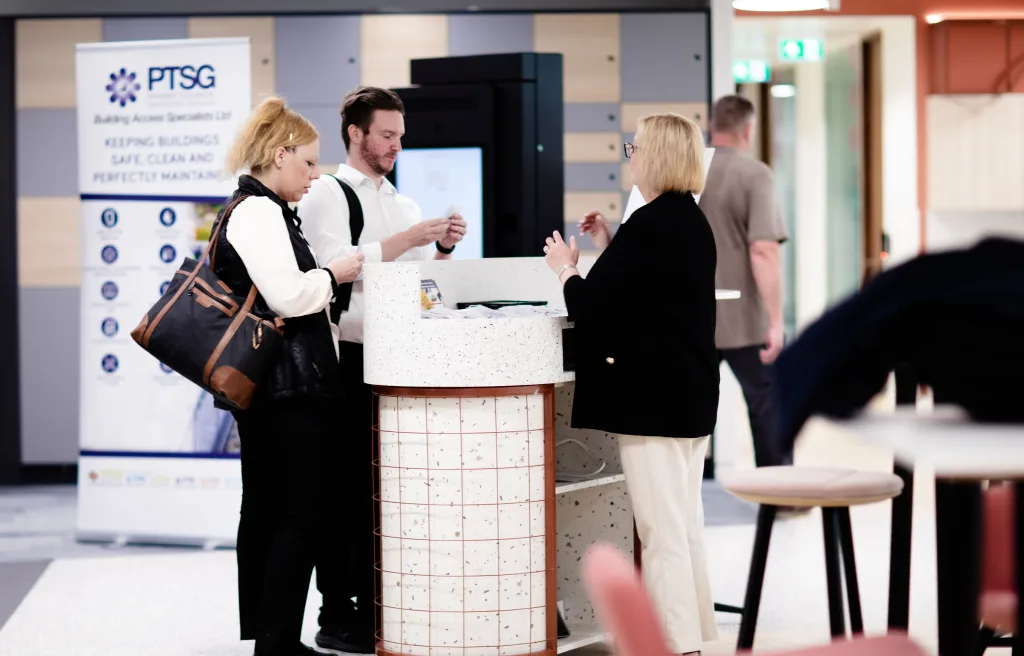